In the world of advanced manufacturing, CNC squirt has emerged as a game-changing technology. It represents a sophisticated approach to machining, offering unparalleled precision and efficiency. Whether you're in the automotive, aerospace, or electronics industry, this technology has become indispensable. CNC squirt combines cutting-edge software with highly precise machinery to deliver results that were once thought impossible.
As industries continue to evolve, the demand for accuracy and speed in production has never been higher. CNC squirt stands out as a solution that addresses these needs effectively. Its ability to execute complex designs with minimal errors has positioned it at the forefront of modern manufacturing techniques.
In this comprehensive guide, we will delve into the intricacies of CNC squirt, exploring its applications, advantages, limitations, and future potential. Whether you're a manufacturer looking to optimize your processes or simply curious about the technology, this article will provide all the insights you need.
Read also:Xxmx
Table of Contents
- What is CNC Squirt?
- History of CNC Squirt
- How CNC Squirt Works
- Applications of CNC Squirt
- Advantages of CNC Squirt
- Limitations of CNC Squirt
- Materials Used in CNC Squirt
- Maintenance of CNC Squirt
- Cost Analysis of CNC Squirt
- Future of CNC Squirt
What is CNC Squirt?
CNC squirt refers to a specialized form of computer numerical control (CNC) machining that focuses on precision fluid delivery systems. Unlike traditional CNC machining, which primarily involves cutting and shaping solid materials, CNC squirt is designed to handle liquid or semi-liquid substances with extreme accuracy. This technology is essential in industries where the controlled application of fluids is critical, such as in the production of fuel injection systems, hydraulic components, and medical devices.
Key Features of CNC Squirt
- Precision control over fluid flow rates
- Ability to handle a wide range of materials, including adhesives, lubricants, and resins
- Integration with advanced software for automated processes
- High repeatability and consistency in output
The integration of CNC squirt into manufacturing processes has significantly improved product quality and reduced waste. By automating the fluid application process, manufacturers can achieve higher levels of accuracy and efficiency, ultimately leading to cost savings and increased productivity.
History of CNC Squirt
The development of CNC squirt can be traced back to the advancements in CNC machining during the mid-20th century. As industries began to demand more precise and automated solutions, engineers started exploring ways to adapt CNC technology for fluid handling applications. The first CNC squirt systems were introduced in the 1980s, primarily for use in the automotive industry.
Milestones in CNC Squirt Development
- 1980s: Initial development of CNC squirt systems for automotive fuel injection
- 1990s: Expansion into aerospace and medical industries
- 2000s: Integration of advanced software and sensors for improved accuracy
Today, CNC squirt continues to evolve, driven by advancements in artificial intelligence, machine learning, and IoT technologies. These innovations have further enhanced its capabilities, making it an indispensable tool in modern manufacturing.
Read also:Carrie Preston
How CNC Squirt Works
CNC squirt operates by using a combination of software and hardware to control the precise application of fluids. The process begins with the design of the desired pattern or shape using CAD software. This design is then translated into machine-readable code, which is fed into the CNC controller. The controller directs the movement of the squirt head, ensuring that the fluid is applied exactly where it is needed.
Components of a CNC Squirt System
- CNC Controller: The brain of the system, responsible for interpreting the design and directing the squirt head
- Squirt Head: The component that applies the fluid to the target surface
- Fluid Reservoir: Stores the fluid to be applied
- Sensors: Monitor the process to ensure accuracy and consistency
The precision of CNC squirt is achieved through the use of advanced algorithms and real-time feedback systems, allowing for adjustments to be made during the application process. This ensures that even the most complex designs can be executed with minimal errors.
Applications of CNC Squirt
CNC squirt finds applications in a wide range of industries, each benefiting from its precision and versatility. Some of the key industries include:
Automotive Industry
In the automotive sector, CNC squirt is used for fuel injection systems, brake systems, and engine assembly. Its ability to apply fluids with exacting precision ensures optimal performance and reliability of automotive components.
Aerospace Industry
The aerospace industry relies on CNC squirt for the production of hydraulic systems, fuel systems, and other critical components. The high standards of accuracy required in aerospace manufacturing make CNC squirt an ideal solution.
Medical Industry
In the medical field, CNC squirt is used for the production of implants, prosthetics, and other medical devices. Its precision ensures that these devices meet the strict regulatory requirements of the industry.
Advantages of CNC Squirt
CNC squirt offers numerous advantages over traditional fluid application methods. Some of the key benefits include:
- Increased Precision: CNC squirt ensures that fluids are applied with exacting accuracy, reducing errors and improving product quality.
- Improved Efficiency: Automated processes reduce the time and labor required for fluid application, leading to increased productivity.
- Cost Savings: By minimizing waste and improving efficiency, CNC squirt helps manufacturers reduce costs.
- Enhanced Flexibility: CNC squirt systems can be easily reprogrammed to handle different applications, making them versatile tools in any manufacturing environment.
These advantages have made CNC squirt a popular choice for manufacturers across various industries.
Limitations of CNC Squirt
Despite its many benefits, CNC squirt does have some limitations that manufacturers need to consider. These include:
- High Initial Costs: The upfront investment required for CNC squirt systems can be significant, making it less accessible for smaller businesses.
- Complexity: The technology involved in CNC squirt can be complex, requiring specialized training for operators and maintenance personnel.
- Maintenance Requirements: Regular maintenance is necessary to ensure the system operates at peak performance, adding to the overall cost of ownership.
Manufacturers must weigh these limitations against the benefits when deciding whether to adopt CNC squirt technology.
Materials Used in CNC Squirt
CNC squirt can handle a wide variety of materials, each with its own unique properties and applications. Some of the most commonly used materials include:
- Adhesives: Used for bonding components together in various industries
- Lubricants: Essential for reducing friction and wear in mechanical systems
- Resins: Used in the production of composites and coatings
- Inks: Used in printing and labeling applications
The versatility of CNC squirt in handling different materials makes it an invaluable tool in modern manufacturing.
Maintenance of CNC Squirt
Proper maintenance is crucial for ensuring the longevity and optimal performance of CNC squirt systems. Some key maintenance practices include:
- Regular Cleaning: Keeping the system clean helps prevent clogs and ensures accurate fluid delivery.
- Calibration: Periodic calibration ensures that the system continues to operate within specified tolerances.
- Software Updates: Keeping the software up to date helps improve performance and adds new features.
By following these maintenance practices, manufacturers can maximize the lifespan and efficiency of their CNC squirt systems.
Cost Analysis of CNC Squirt
While the initial cost of implementing CNC squirt can be high, the long-term benefits often outweigh the expenses. A cost analysis should consider factors such as:
- Purchase Price: The cost of acquiring the CNC squirt system
- Maintenance Costs: Ongoing expenses for maintenance and repairs
- Operational Savings: Cost savings achieved through increased efficiency and reduced waste
By conducting a thorough cost analysis, manufacturers can determine the return on investment (ROI) of implementing CNC squirt technology.
Future of CNC Squirt
The future of CNC squirt looks promising, with ongoing advancements in technology driving further improvements. Some of the trends shaping the future of CNC squirt include:
- Integration with AI and Machine Learning: Enhancing the system's ability to learn and adapt to new applications
- Increased Connectivity: Leveraging IoT technologies to improve data collection and analysis
- Advancements in Materials Science: Expanding the range of materials that can be handled by CNC squirt systems
As these trends continue to evolve, CNC squirt is likely to become even more integral to modern manufacturing processes.
Conclusion
CNC squirt represents a significant advancement in precision manufacturing, offering unparalleled accuracy and efficiency in fluid application processes. From its origins in the automotive industry to its current applications in aerospace, medical, and beyond, CNC squirt has proven to be a versatile and valuable tool. While there are challenges associated with its adoption, the benefits it provides make it a worthwhile investment for many manufacturers.
We encourage readers to explore the potential of CNC squirt further and consider how it might benefit their own manufacturing processes. Feel free to leave a comment or share this article with others who may find it useful. For more insights into the world of manufacturing, be sure to check out our other articles on related topics.

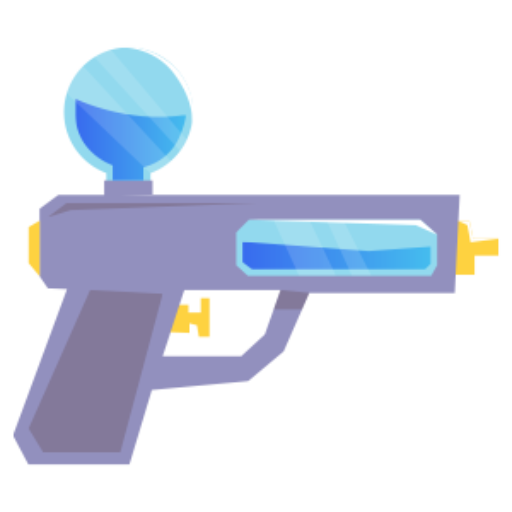